An insulated precast foundation is a construction product that has been produced after the proper mix of concrete, water and other materials are cast into form. It is usually installed in structures especially modular homes to increase energy efficiency and durability. Precast foundation is usually built and cured in factory, but it can be taken on- site.
History of Insulated Precast Foundation
Stepping back into history, it was claimed that the ancient Roman builders were the first time persons to use precast concrete foundation as they construct iconic structures. They utilized concrete by mixing it with other materials and later poured it into the molds to form aqueducts, tunnels and buildings. The Romans were very keen on the materials they were using in the molding of their tangible walls back then. They made sure that the concrete withstands the effects of natural disasters, war, invasion and rebellion.
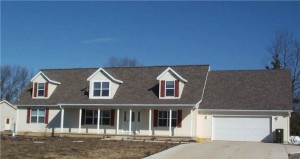
Modular Home with Insulated Precast Foundation
In 1905, the precast paneled buildings came into view in Liverpool, England. The genius idea and works of the city engineer John Alexander Brodie made their way to create the process in making precast panels. And in 1906, tram stables at Walton, Liverpool were erected. Unfortunately, it was not embraced by most of Britain. The idea was later adopted extensively by builders of the Eastern Europe and other parts of the world.
In contemporary times, the realization of an insulated precast foundation came across along with the incorporation of green building techniques. Since then, innovations are made as its use is widely considered to lower the environmental impact of the home. It is also a good way to prevent increasing utility bills per month.
Application of Insulated Precast Foundation to Modular Homes
Today general contractors are incorporating insulated precast foundation when constructing modular homes and saw its used as the answer to the growing demand of having a sturdy and durable basement or walls. The technique employed to construct the precast foundation is not only appealing to them; it is also beneficial for the home builders and home owners.
An insulated precast foundation for modular homes is intricately made in an indoor and controlled environment. Serious monitoring is done by general contractors to assure that it is done in compliance with the standards stated in the building code. Typically, most precast foundation has the maximum insulation rate possible and interior studs that are ready to accept the drywall before it was completed on- site.
Once the precast foundation is in the project site, home builders and his team works on the base, where they crushed and compressed the gravel. They need to ensure that the base is better for the soil and loading conditions. The sections of the precast foundation are then assembled and glued the sections tightly and securely to prevent future leakage of heat, water and other aggregates. Waterproofing and drainage systems are often set up to protect the foundation and the whole structure of the house.
Prefabricated homes greatly benefit from the installation of the insulated precast foundation in many ways. One of which is the regulation of indoor temperature during seasons. Insulated precast walls prevent indoor heat loss during winters and protect the home from excessive heat during summers. Insulated precast foundation also promotes economic savings as it helps govern the use of electrical and HVAC system every day, leaving lower utility bills per month.
Now look for a modular home dealer who works with the incorporation of insulated precast foundation. A wise home buyer starts looking for a modular home dealer with Legendary Homes.
“With its superior quality, energy efficiency, strong and budget friendly modular homes, Legendary Homes is one of the trusted modular home builders around Clarklake and Jackson Michigan for over 20 years of experience now. Legendary Homes helps in site location, acquisition of permits, excavation, foundation (including Insulated Pre-Cast Foundations), landscaping, breeze ways and other services needed to complete your home. As a company that prioritizes its customers, Legendary Homes allows you to customize your home. And most importantly, we assist in modular homes financing by working with the top lenders in Michigan.”
It’s amazing news to start building your dream home, right? “We can make your dreams a reality!”
Topic: Insulated Precast Foundation